Although PV produces electricity from sunlight with no emissions, it is not “free.” It requires energy, resources, transportation, and installation, all of which are processes currently require carbon emissions.
In pursuit of reduced emissions, one of the major drivers of solar adoption, along with reduced costs, component procurers and project developers must consider the carbon required to bring a project to fruition. Sometimes referred to as the “carbon backpack,” the embodied carbon in a component can differ greatly based on materials used and where it was produced.
According to the Ultra Low-Carbon Solar Alliance, the use of PV materials with a lower carbon backpack can reduce the carbon footprint by 50% in the U.S. and 70% in Europe.
Origami Solar, a designer and manufacturer of recycled steel frames for solar modules, commissioned an independent study with Boundless Impact Research & Analytics to understand the difference in carbon backpack between its product and leading competitors. The analysis considered raw material production, manufacturing, transportation, and more.
It found that compared with traditional virgin material aluminum module frames shipped from China, U.S.-made module frames made from recycled steel show a 90.4% reduction in greenhouse gas emissions. In Germany, the frames have a 94.7% carbon advantage.
Boundless estimates the greenhouse gas footprint of Origami Solar’s steel module frames at 9.25 kilograms (kg) of carbon dioxide equivalent per 2 meter by 1 meter frame produced in the U.S.
“The estimated Fossil Energy Footprint of Origami Solar’s steel module frame is 71.8 megajoules (MJ) in the United States and 62.2 MJ in Germany per 2 by 1-meter frame, compared to 920 MJ for a conventional virgin aluminum frame produced in China using an extrusion production process,” said the report.
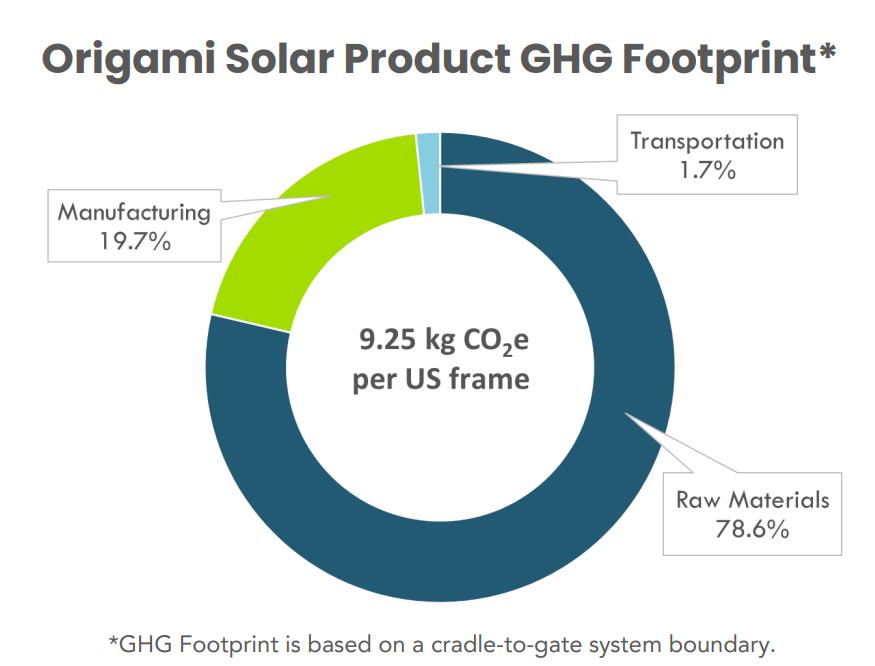
The company said the improved carbon embodiment would result in a reduction of 80 kg of emissions per module or 200 metric tons per MW.
Analysis by Bloomberg NEF found that though solar component costs have lowered, aluminum framing has stayed relatively flat, and now represent about 25% of the cost of a module.
Find the full comparative analysis and learn more about Origami’s process here.
Origami Solar, a small company based in Bend, Oregon, was awarded the grand prize in the 2022 U.S. Department of Energy’s American-Made Solar Prize competition, recognizing the disruptive value and market potential of the company’s steel module frame.
The company said it is sourcing steel and plans on producing frames regionally, thus eliminating supply chain constraints and trucking miles. The company reports that the frames are 100% U.S. made and will enable solar modules to qualify for the domestic content bonus tax credit.
“Steel is an earth-abundant resource that can be manufactured on every continent, the use of which in trackers, racking, mounts, and tubes is already widely accepted by the solar industry,” said Mathew Arnold, chief executive officer of Unimacts, a Boston-based manufacturer with production facilities in Nevada, Mexico and Spain. “We are excited to collaborate with Origami Solar to rapidly facilitate the shift from imported aluminum to domestically made steel frames.”
This content is protected by copyright and may not be reused. If you want to cooperate with us and would like to reuse some of our content, please contact: editors@pv-magazine.com.
By submitting this form you agree to pv magazine using your data for the purposes of publishing your comment.
Your personal data will only be disclosed or otherwise transmitted to third parties for the purposes of spam filtering or if this is necessary for technical maintenance of the website. Any other transfer to third parties will not take place unless this is justified on the basis of applicable data protection regulations or if pv magazine is legally obliged to do so.
You may revoke this consent at any time with effect for the future, in which case your personal data will be deleted immediately. Otherwise, your data will be deleted if pv magazine has processed your request or the purpose of data storage is fulfilled.
Further information on data privacy can be found in our Data Protection Policy.